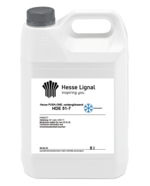
PURA-ONE HDE 51-x(gloss level)
PURA-ONE HDE 51-x(gloss level) is characterized by a particularly abrasion-resistant and tough-elastic surface, which also has very good chemical resistance. The transparent 2C HYDRO topcoat is also powerfull filling and light fast. The product's wide range of applications extends from coating wooden stairs to sealing of parquet in ship interiors. The product can be used on bleached wood. For parquet and wooden floors with a tendency to side and block gluing, the combination with the brightening primer HG 21 or with the scorching primer HG 22 is recommended. The lacquer material is certified according to IMO.
Enquire articlePage content
- Light-fast
- Good transparency
- Certified according to IMO so it can be applied on ship interiors
Processing
- water 54%
- mineral resources 1%
- fossil resources 45%
Areas of application
For parquet flooring, wood and OSB floors that are subjected to high demands. Can also be used on bleached surfaces (that are adequately dry).
Technical information
Sustainability data sheet
Certificates
Technical Specifications
Appearance | colourless |
---|---|
Decopaint base | wb |
Decopaint category | I |
Number of layers (max) | 2 |
Quantity per layers (min) | 80 g/m² |
Quantity per layers (max) | 100 g/m² |
Total quantity applied | 200 g/m² |
Mixing ratio (volumetric) | 10 : 1 | Hardener: HDR 71 |
Mixing ratio (gravimetric) | 100 : 10 | Hardener: HDR 71 |
Processing Instructions
Potlife | 3 h / 20 °C |
---|---|
Drying | 3 h / 20 °C |
Due to hardening | 7 d / 20 °C |
Surface sanding (grain size) | 100 - 120 |
Intermediate sanding (grain size) | 120 - 150 |
Yield per pass | 9 m²/l |
Processing information | The floor must first be sanded back to the bare wood and be dry and free from oil, grease, wax, silicones and sanding dust. For renovation or repairs of previously sealed surfaces: Perform a test coating to determine whether the current substrate can be sealed with PURA-ONE. After suitable drying, test the bonding of the complete coating! Shake the lacquer well! Add the correct hardener to the organic lacquer container and immediately shake well for 1 - 2 min. Do not mix in the application container. The mixing ratio must also be accurately observed in the case of partial amounts, and the mixture well shaken. Press the strainer into the outlet opening, fill the lacquer / hardener mixture into a suitable application container and work from this! Only use a mixture within the given application time. Never store product mixed with hardening agent in closed containers. Do not use any electrical stirring devices; risk of forming foam or bubbles! Clean work equipment with water.. Dried lacquer residue can be removed with Hesse CLEANING-AGENT DV 9. |
Special notes | To achieve “R10” slip resistance according to DIN 51130 you need to add 10 % of Hesse HZ 75 anti-slip additive to the final sealing coat! Please shake / stir the additive in well.] [Critical substrates such as wood block, on-edge lamellar parquet, floor boards, parquet flooring on underfloor heating, etc. require proper pre-treatment with HG 22 to minimise the risk of lateral bonding.] [To avoid the possibility of staining, please only renovate parquet flooring, which was previously treated with solvent-based systems, with solvent-based systems again!] [Clean work equipment with water.] [Dried lacquer residue can be removed with Hesse CLEANING-AGENT DV 9. Films or carpets must not be placed on the parquet flooring until it has completely hardened.] [Shake the lacquer well! Spraying: possible; however the addition of water is required. When the hardening agent is well worked in, adjust the spraying viscosity with up to 5 % water. Personal protective equipment and adherence to the instructions for the spraying application.[This product must only be combined with other approved and technically suitable products when used as a flame retardant coating material for seagoing vessels according to the latest version of SOLAS 74 Reg. II-2/3, II-2/5, II-2/6 and X/3, as amended, IMO Resolution MSC.36(63)-(1994 HSC-Code) 7, IMO Resolution MSC.97(73)-(2000 HSC-Code) 7, IMO MSC/Circ. 1120. The maximum application amount in wet film when using this product as a flame retardant coating material for seagoing vessels is] 2 x 100 g/m². “A risk assessment was undertaken according to Directive 2014/90/EU, Annex II, Section 3. This coating does not pose a physical risk to health nor a risk to the environment when cured and dried.” |
Procedure example
Our technical information is continually adapted to keep up to date with the latest technology and statutory regulations. The latest version is always available online at www.hesse-lignal.de or talk to your local account manager. This information is for advice and is based on the best knowledge available and careful research in line with the current state of the art. This information cannot be held as legally binding. We also refer you to our terms and conditions of business. Safety data sheet is provided in accordance with EC regulation no. 1907/2006.
Request a series
<% headline %>
Your request for the article

Your request for the series
