Surfaces with the highest level of resistance
Use calander coating for high-quality and low-cost coating solutions
Calander coating is often used in the wood-based materials industry to produce cost-effective coatings that still meet the highest quality standards.
Which problems does the procedure solve? Complex process steps are often required after the actual wet lacquer coating if you want to introduce certain textures onto surfaces. Perfect high-gloss surfaces, for example, require adapted polishing processes. Textures can range from extremely smooth (high gloss) to rough (matt lacquer). Integrated into the wet coating, this technology prevents that additional effort and thus creates comparable effects at low cost.
The advantages at a glance
Surfaces from matt to high gloss are achievable with calander coating
How calander coating works
What does this technology do and how does it work?
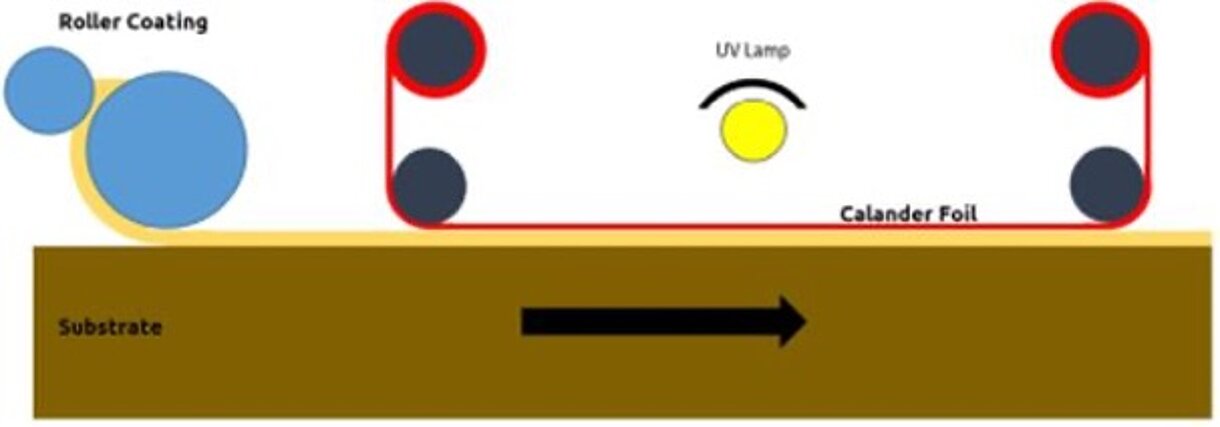
How calander coating works
What does this technology do and how does it work?
The timber industry saw
calander coating
being invented to produce inexpensive coatings with superior quality.
This procedure involves a plastic film being laid onto the wet lacquer film. The lacquer film is subsequently hardened using UV light that shines through the plastic film. Either a perfect high gloss surface or a matt, micro-textured surface is obtained after removing the plastic film, depending on the plastic film’s characteristics.
Since the radiation is inert, i.e. occurs in an oxygen-free environment, the finished surface meets the highest demands in terms of scratch
resistance
.
Contact partner
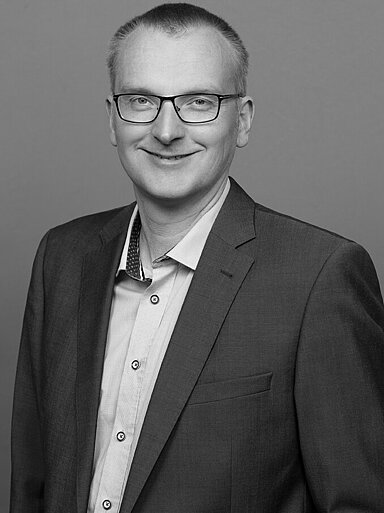
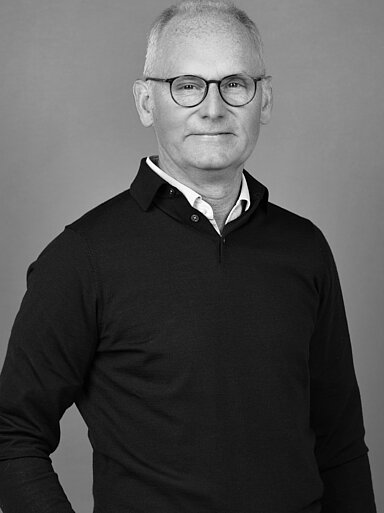
Conrad