Create concrete-look surfaces with sustainable components.

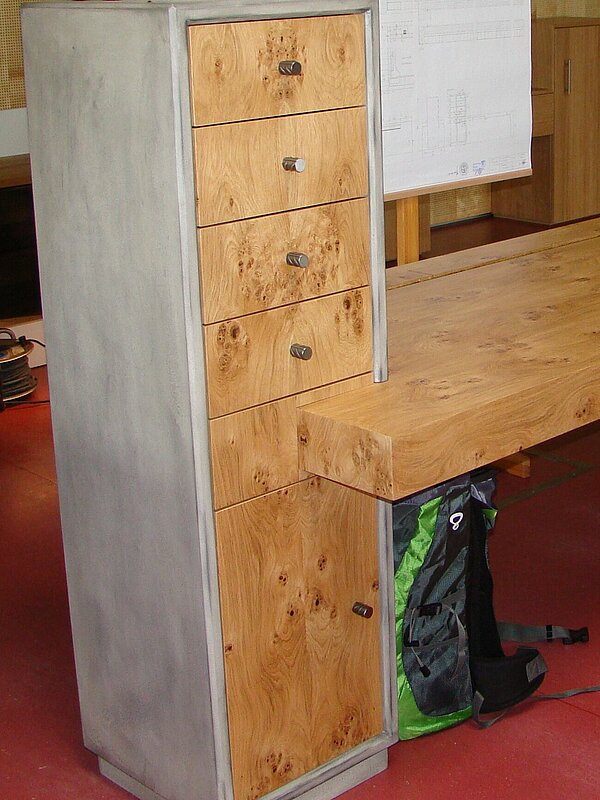
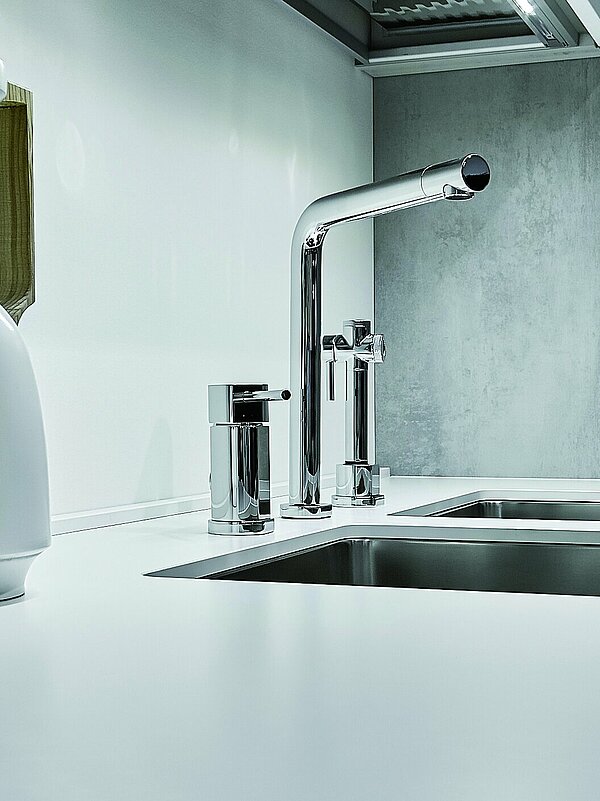
Create concrete-look surfaces with sustainable components.
The HYDRO concrete effect makes it possible to create surfaces that are deceptively similar to real concrete, even in the long term. Almost all substrates can be coated with concrete effect and the effect does not require the addition of cement powder. There are no limits to the appearance of the desired effect. The HYDRO concrete effect can be painted, filled and manually finished. Workpieces can be painted that would be difficult to produce with real concrete and are also much lighter. With this effect, every surface becomes an individual and high-quality unique piece.
Fields of application : Interior fittings and furniture
How to HYDRO Concrete effect
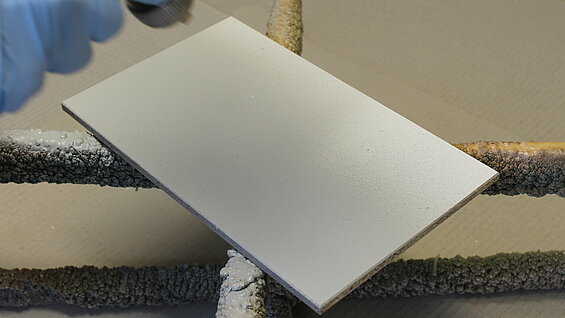
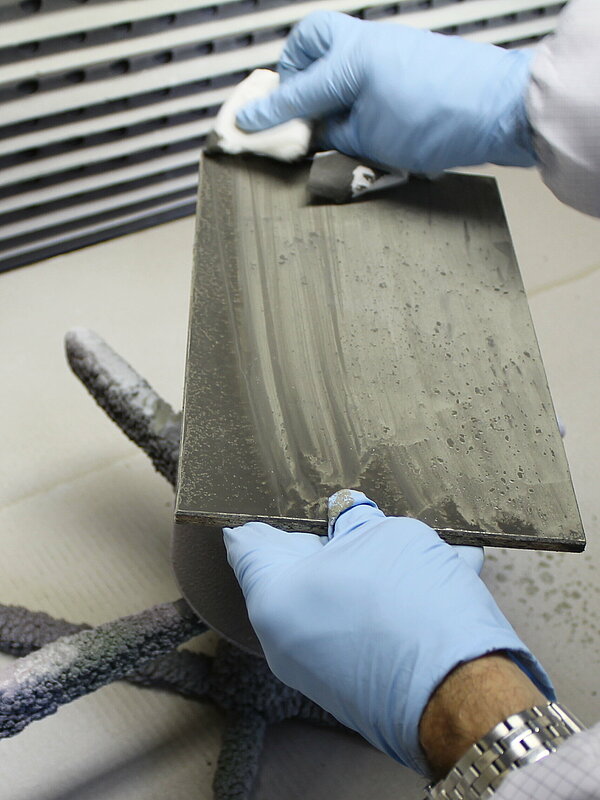
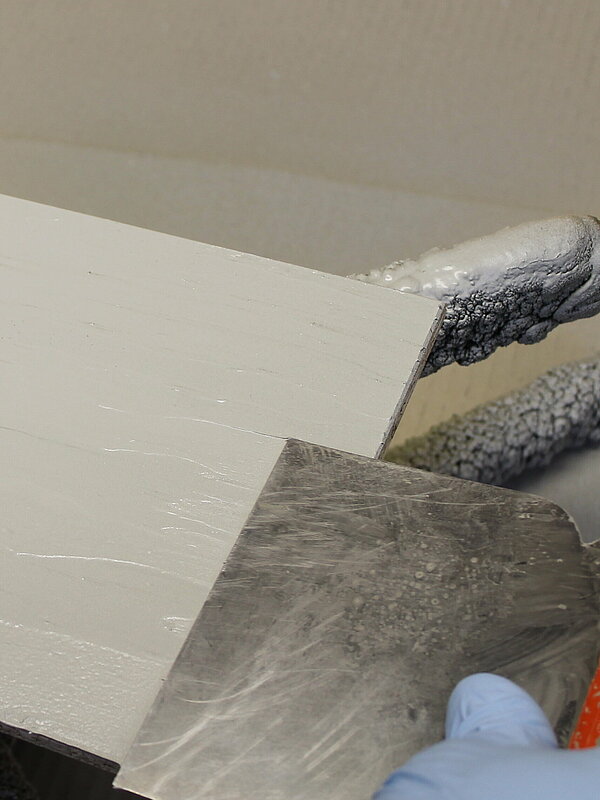
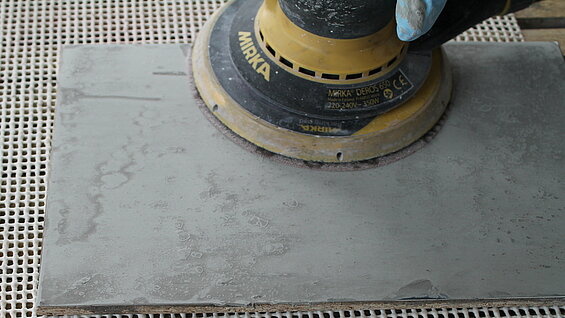
How to HYDRO Concrete effect
- Sand the desired substrate material (e.g. FPY or MDF priming foil or melamine resin foil) well. We recommend sanding with grit 150 - 240. Depending on the desired effect, we recommend filling beforehand when using a raw MDF surface or edge to achieve a more homogenous surface. If possible, dry this filler layer overnight at 20 °C room temperature. Then sand with 280 - 400 grit immediately before further coating.
- Depending on the pigment filler chosen, add up to 5 % of HZ 71 brush-on paint additive to obtain the desired viscous working condition. For a particularly authentic effect, approx. 5 % Hesse colour concentrate HF G1651 can be added. The additives are stirred in with a stirring rod until they have spread homogenously. When using an electric stirrer, please ensure that no air is incorporated into the paint; therefore, let it run slowly.
- Then add the prescribed hardener and mix it in intensively.
- The filler mixture prepared in this way is applied to the substrate either in a rich amount with a cup gun or directly with a putty knife and, if necessary, after a short anti-drying phase, worked to effect with the putty knife, a brush or another tool, depending on the desired effect.
- Then allow a drying time of at least 16 hours at a room temperature of approx. 20 °C (depending on the pigment filler used and the coat thickness applied, even longer if necessary).
- Sand the Surface for effect. If smooth surfaces are desired, use a grit of approx. 320, and if rougher surfaces are desired, use correspondingly coarse sanding paper.
- After removing the sanding dust, apply the Hesse colour stain BC 85-22881 (with the cup gun), which has been specially adapted to this method of working, in such a way that after a short reaction time the surplus is removed from the Surface with a cloth and the desired effect is worked out. The areas where more stain remains on the Surface will look darker than the areas where more stain has been removed.
- After the stain has dried for at least 1 hour at 20 °C room temperature, the Surface can be top coated. For this purpose, either Hesse PERFECT-TOP HDE 54002, mixing ratio 10 : 1 with HDR 5091 or Hesse HYDRO-PU Natural Wood Effect HDE 54500-0001, mixing ratio 10 : 1 with HDR 5081 should preferably be used (depending on the desired resistance of the surface).
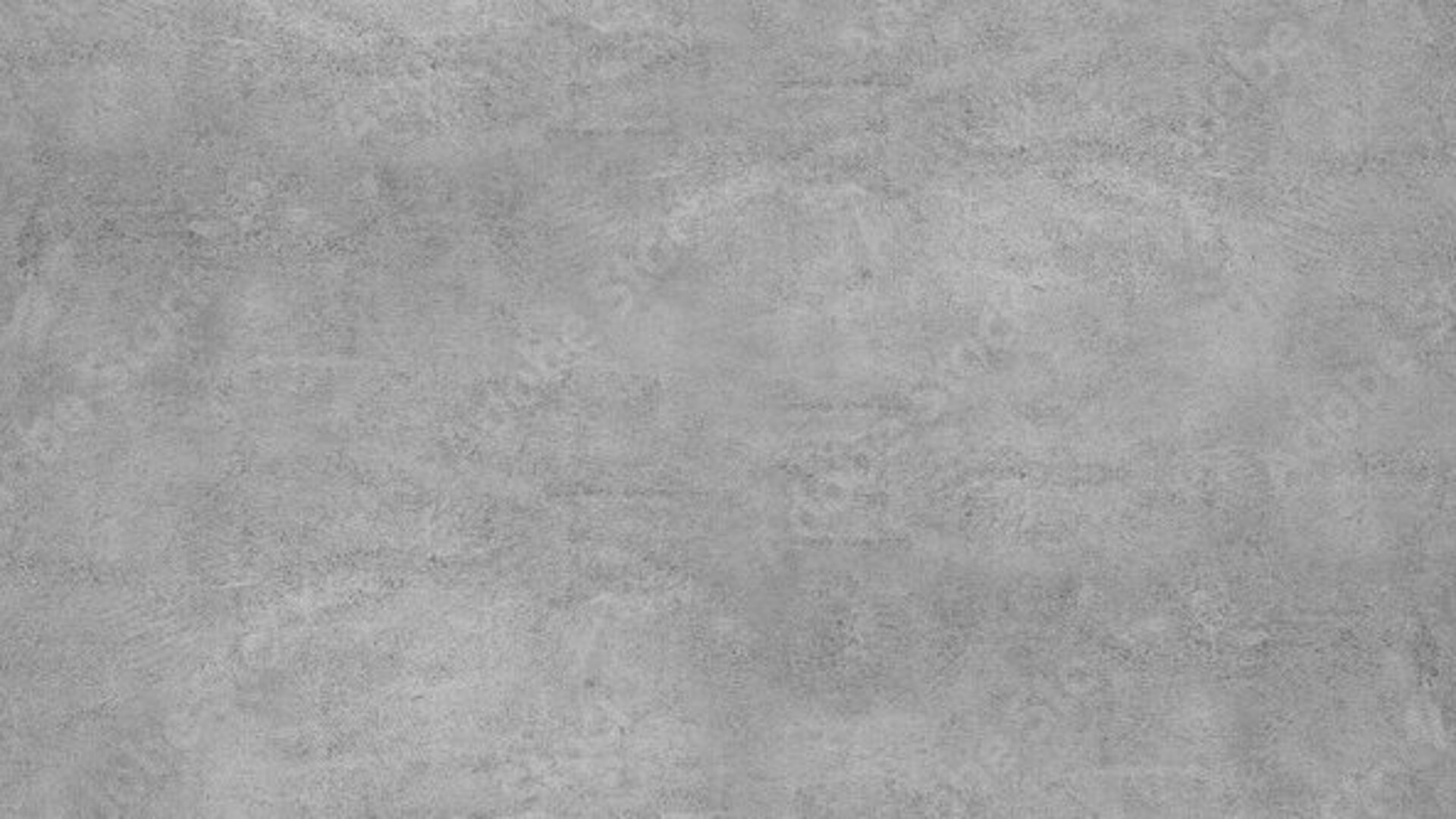
Technical Information HYDRO Concrete Effect
Products required
Note
Please observe the latest technical information and material safety data sheets of the individual products listed. Special instructions: PU varnishes should not be processed and dried at material and room temperatures below 18 °C. To avoid adhesion problems, PU lacquer surfaces should be freshly sanded before the Finish is applied.
Attention: Please note the exact hardener and thinner additions in the following information.
NoteThe information provided is of an advisory nature and is based on the best of our knowledge and careful research according to the current state of the art. A legally binding character cannot be derived from this information. Please also refer to our terms and conditions. Material safety data sheet according to Regulation (EC) No. 1907/2006 is provided.
Contact partner
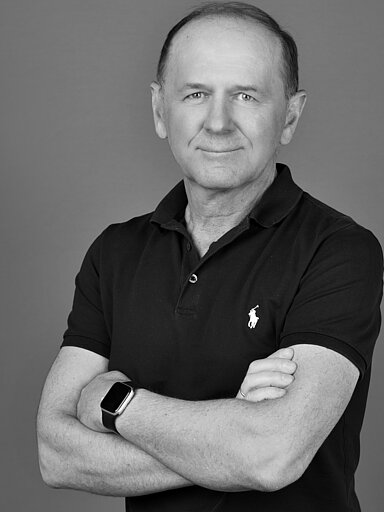